某烘焙企业曾因一批次产品过期导致客户投诉,追溯时发现生产日期与原料批次对应关系缺失,质检数据分散在3个系统中——这种场景揭示了食品行业质量成本控制的深层矛盾:质量损失往往源于数据割裂而非技术缺陷。优德普的食品加工ERP方案,正通过全链路数据穿透与动态根因分析,将质量管控从“被动止损”转向“主动预防”。
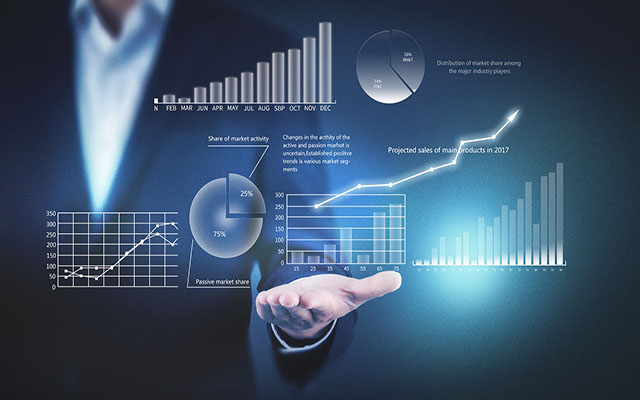
智能追溯:穿透供应链的“数据显微镜”
1.正向追溯:输入成品批次号,10分钟内可反查原料供应商、生产工单、工艺参数及质检报告。某肉制品企业曾借此快速锁定某批次包装材料密封性不足导致的保质期缩短问题。
2.反向拦截:当某原料检验不合格时,系统自动冻结关联在制品与库存成品,避免问题扩散至下游环节,某乳企借此将原料异常处理时效提升40%。
3.合规性强制管控:在灭菌、灌装等关键节点设置数据录入屏障,未完成质检流程无法流转至下道工序,确保HACCP、ISO22000等标准落地。
对比手工管理模式,优德普方案将召回成本降低65%,飞检报告生成效率提升80%。
不合格品分析:从表象治理到根因挖掘
1.多源数据聚合:整合设备日志(如油炸温度曲线)、环境监测数据(车间温湿度)、人工检验记录(感官评价),构建质量数据全景视图。某休闲食品企业通过分析发现,包装机温度波动与真空度不合格率呈强相关性。
2.根因关联模型:基于知识图谱技术,建立“设备参数—工艺标准—人员操作”的关联规则库。当灌装速度提升15%时,系统自动检查封口完整性数据是否异常,某饮料厂商借此将灌装不良率从3.2%降至0.8%。
3.成本穿透核算:不合格品损失自动关联至原料成本、人工工时、能源消耗等维度,生成质量成本热力图。某企业发现外包杀菌环节的质量损失占总成本的31%,遂将部分工序转为自营,年节约成本超200万元。
相较于传统“事后归因”模式,优德普方案通过实时数据驱动,使质量问题发现周期从周级压缩至小时级。
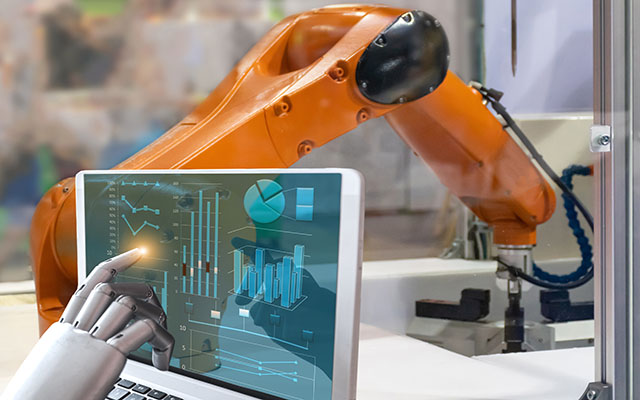
协同效应:质量数据与业务流的闭环
1.生产计划联动:当某原料批次不合格率超过阈值时,系统自动调整生产排程,优先使用替代物料,某速冻食品企业借此减少停工损失15%。
2.供应商协同:不合格品信息实时同步至供应商门户,触发整改任务并关联采购合同条款。某烘焙原料供应商因连续3批次水分超标被系统自动降级,采购转向率提升22%。
3.成本动态预警:质量损失超预算时,自动触发跨部门会议通知,推动技术、生产、采购联合制定改善方案。某调味品企业通过此机制,将月度质量会议决策效率提升50%。
这种“质量数据驱动业务决策”的机制,使企业从“单一问题解决”转向“系统性质量生态”构建。
1.显性成本优化:手工报表工作量减少60%,质检异常响应时间从48小时缩短至4小时,库存过期损失率下降35%。
2.隐性能力沉淀:历史质量数据转化为预测模型,为新品开发提供风险预判。某企业拓展低温短保产品线时,系统自动提示包装材料耐冷性测试要求,避免上市后批量质量问题。
关于宁波优德普>>>
了解更多SAP ERP管理系统成功案例>>>
或拨打宁波优德普免费咨询热线:400-8045-500