工厂车间里跳动的电表数字,曾是许多管理者心中的"无底洞"。双碳政策下,这份焦虑被进一步放大——既要满足产能需求,又需应对阶梯电价与碳配额压力。优德普SAP ERP能耗管理模块的实践表明,通过重构数据采集、分析、决策的闭环逻辑,企业完全能在不牺牲生产效率的前提下,实现年均15%的用电成本优化。
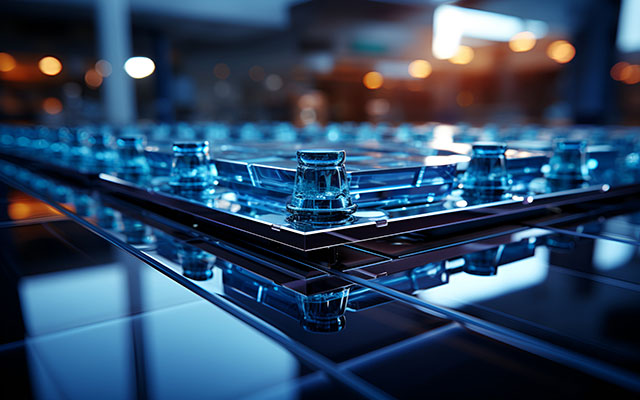
一、数据穿透:让能耗"看得见"的底层逻辑
技术差异化体现在两方面:
1.动态基准模型:内置化工行业通用能效模型,自动比对同类产线标准值,如某化工厂通过对比发现干燥工序电耗超标23%,针对性改造后单月节电8万度;
2.异常预警机制:当设备电流波动超过设定阈值时,系统自动触发检修工单。某涂料企业曾因电机轴承磨损导致日耗电增加5%,系统在24小时内识别异常并推送预警,避免持续损耗。
二、智能调度:打破生产与用电的割裂状态
1.时间维度:自动匹配电价低谷与生产高峰,如将离心机批量作业调整至夜间低价时段,某化纤企业借此降低12%用电成本;
2.空间维度:对于多厂区企业,系统根据各区域供电稳定性动态分配产能。网页3提到的"生产与物流协同"理念在此延伸,通过优化能源传输路径减少线损。
与传统ERP的静态排程相比,该模块的突出价值在于实时响应。当突发停电或电价政策调整时,系统能在20分钟内重新计算排产方案,确保用电成本可控。
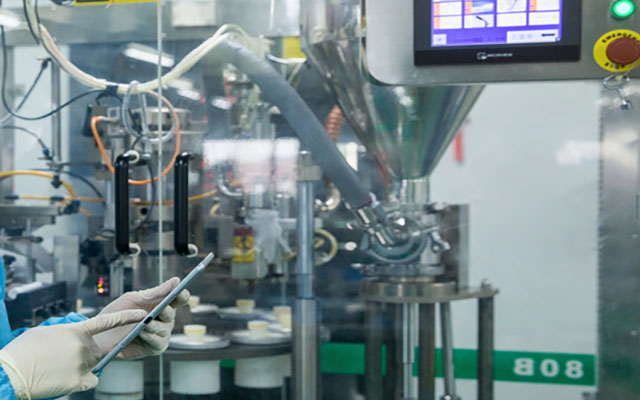
三、设备治理:从救火式维修到预防性优化
1.能效画像:基于历史运行数据构建设备能效曲线,量化性能衰减程度;
2.预测维护:结合AI算法预判故障风险,如某氯碱厂通过提前更换低效泵体,年节省维护成本40万元;
3.改造决策:自动生成能效改造建议清单,优先显示投资回收期<2年的项目。
这种"数据驱动+经验沉淀"的模式,将设备管理从依赖老师傅经验的阶段,升级为可量化的持续改进流程。
四、成本溯源:让每度电的流向都有据可依
1.产品维度:按反应方程式计算单位产品的理论电耗,与实际值对比分析;
2.工艺维度:区分连续生产与间歇作业的能耗差异,识别非必要工艺环节;
3.环境成本:自动将电耗转换为碳排放量,满足ESG披露需求。
某新材料企业通过该模块发现,某产品灌装环节电耗占比达28%,经工艺优化后单线年节电15万度。这种透明化核算机制,为管理层提供了可靠的决策依据。
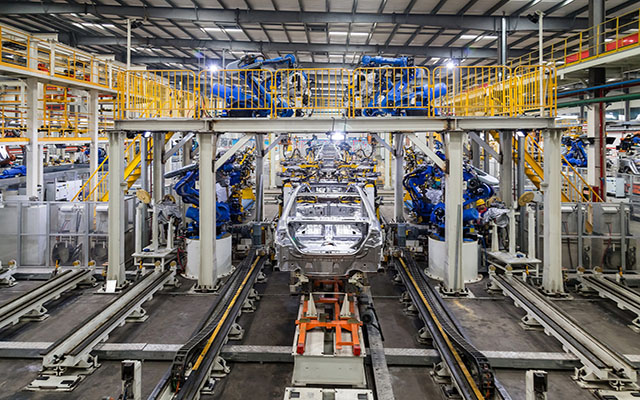
1.云端快速部署:基于SAP Business ByDesign平台,3周内上线基础监控功能,适合中小型企业试水;
2.本地深度开发:支持ABAP定制开发,满足多厂区数据聚合、复杂审计报表等需求,如网页6中化工企业实现的"全流程质检联动能耗分析"。
不同于"一刀切"的改造模式,企业可优先部署实时监控模块,再分阶段扩展至调度优化。某案例显示,分步实施使初期投入降低65%,而阶段性收益又为后续升级提供资金支持。
能耗管理的本质是数据觉醒
当每一台设备的用电曲线都被准确刻画,当每一笔电费支出都能追溯至具体工序,工厂管理者便拥有了与用能成本对话的资本。优德普的实践揭示了一个真理:双碳目标不是单纯的成本压力,而是倒逼企业重新审视能源价值的契机。通过模块化、渐进式的数字化改造,那些曾被视为"必要损耗"的电费支出,正在转化为可测量、可优化、可管理的战略资源。
关于宁波优德普>>>
了解更多SAP ERP管理系统成功案例>>>
或拨打宁波优德普免费咨询热线:400-8045-500